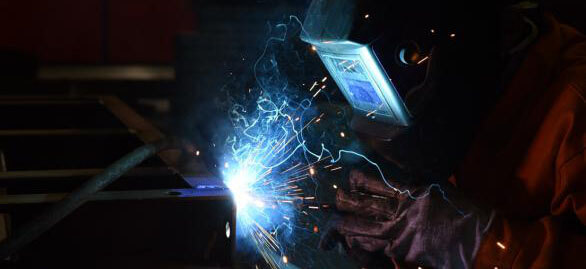
Welding is a process of joining two or more parts by the application of heat and (or) pressure, such joints are permanent in nature. Usually coalescence is achieved by fusion. Very often filler metals are used during welding. More than 50 different welding processes available today. Some are very popular among the industries such as SMAW, GMAW, GTAW, SAW, FCAW etc. whereas some are very specific and limited to few industries such as USW, RSW, DW etc.
SAW (Sub Arc): This process uses a solid electrode submerged in flux. When the wire touches the metal, current is passed through the wire and melts, or "welds", the joint together and the top of the weld os covered in flux. Sub Arc is most commonly used for long seams and round seams.

GMAW (MIG): This process uses a solid electrode. There is no flux, crust, or slag associated with this welding process. It only requires a shielding gas that protects the weld. Short circuit MIG is most commonly used for open groove root welding only- pipe to pipe, pipe to flange, or root welds. Spray mode is used for filling grooves, nozzle insertion welds, and fillet welds. Pulse mode is used for groove welding and attachment welding.
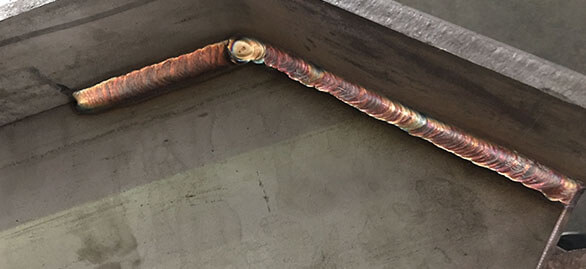
GTAW (TIG): This welding process uses a piece of tungsten that is inside of a "cup". A shielding gas covers the tungsten while welding. While the tungsten is "hot and arcing", the filler metal is dipped into the weld pool. TIG welding is good for root pass welding and groove welding on pipe.

ERW: This process refers to a group of welding processes such as spot and seam welding that produce coalescence of faying surfaces where heat to form the weld is generated by the electrical resistance of material combined with the time and the force used to hold the materials together during welding.
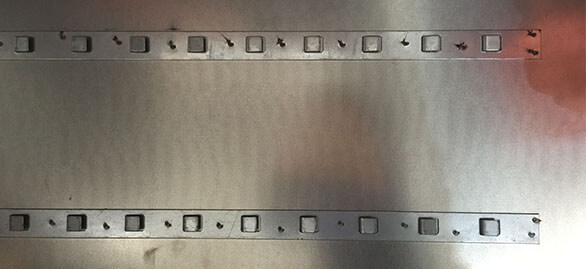
SVEI are ISO 9001 & ISO 3834-2 certificated, and welding operatives are trained and EN ISO 9606-1 certificated. We provide the highest quality according to the QA/QC department and standards. Heavy duty fabrication requires using the correct type of welding to ensure structural integrity. MIG, TIG and many other welding formats are available to compliment the specific types of metals and thicknesses that you will require to produce the equipment you need. Our fabrication capabilities are endless and can span across industries including oil & gas, gas processing, cryogenics, chemical, petrochemical, aerospace, power generation, emission control, and carbon black. For instance, welding has changed the frameworks of many buildings by offering a more solid foundation than rivet construction. Not only is welded steel safer, it is also cost effective.